Exploring the Latest Innovations and Techniques in Welding Jigs
By:Admin
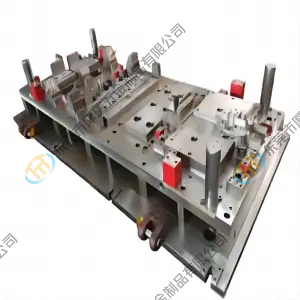
Introduction:
In the realm of industrial manufacturing, precision and efficiency are paramount. Achieving high-quality welds swiftly and accurately is a challenge that companies face daily. However, with the advent of cutting-edge welding jigs, a game-changing solution has emerged. A leading manufacturing company, which we shall refer to as Company XYZ, has recently unveiled their innovative range of welding jigs. With their advanced technology and commitment to excellence, Company XYZ is poised to revolutionize the manufacturing sector.
Company XYZ: Pioneering a New Era in Welding Jigs
With years of extensive research and development, Company XYZ has become a pioneer in the manufacturing industry. Focusing on delivering state-of-the-art tools and equipment, Company XYZ has gained a reputation for its commitment to precision, durability, and cost-effectiveness. Their newest line of welding jigs embodies these values, promising to streamline welding processes and boost productivity for manufacturers across various sectors.
Unveiling the Advantages of Company XYZ's Welding Jigs
Welding jigs play a critical role in ensuring accuracy and uniformity throughout the welding process, enhancing the overall strength and durability of assembled products. Company XYZ's welding jigs offer a myriad of advantages:
1. Uncompromised Precision: Precision is the foundation of any successful welding process. Company XYZ's welding jigs are meticulously designed with engineering precision, guaranteeing an extremely high degree of accuracy. The jigs provide a stable and reliable framework, eliminating the risk of distortion during welding and resulting in impeccable welds with tight tolerances.
2. Increased Efficiency: With Company XYZ's welding jigs, manufacturers can significantly reduce the production time required for complex weldments. The jigs allow operators to securely position and hold workpieces, enabling seamless and continuous welding operations. By leveraging these innovative jigs, manufacturers can optimize their production lines and achieve remarkable time savings.
3. Versatility and Adaptability: Recognizing the diversity of manufacturing needs, Company XYZ's welding jigs are adaptable to various applications. From automotive manufacturing to aerospace industries, these jigs can accommodate a wide array of processes and accommodate different workpiece sizes and shapes. This versatility eliminates the need for multiple jigs, promoting cost-effectiveness and flexibility.
4. Quality Assurance: Company XYZ's welding jigs are designed to ensure consistent weld quality. The jigs' precise alignment and stability significantly reduce the risk of weld defects, such as distortion, porosity, or discontinuities. This quality assurance minimizes rework and ensures the delivery of robust, reliable, and defect-free products.
5. Ergonomic Design: Company XYZ prioritizes the safety and comfort of operators. Their welding jigs incorporate ergonomic features that simplify the positioning and manipulation of workpieces. By minimizing physical strain on operators, these jigs enhance workplace efficiency and reduce the risk of occupational hazards.
Looking Ahead: The Future of Welding Jigs
With the introduction of Company XYZ's revolutionary welding jigs, the future of industrial manufacturing looks promising. As technology continues to advance, welding processes will become even more precise, efficient, and adaptable. The innovative approach of Company XYZ, combined with their commitment to continuous improvement, highlights a vision of manufacturing excellence that is sustainable, competitive, and socially responsible.
In conclusion, Company XYZ's advanced welding jigs have the potential to transform the manufacturing landscape. By increasing precision, efficiency, and versatility, these jigs empower manufacturers to optimize their processes and deliver superior-quality products. As industries embrace these cutting-edge tools, the possibilities for innovation and growth in the manufacturing sector are seemingly boundless.
Company News & Blog
Innovative Tool Enhances Plate Presentation for Food Displays
Add Plate Up In tool is a groundbreaking and innovative software developed by a leading technology company. This cutting-edge tool is set to revolutionize the way individuals and businesses prepare and present their meals.With its advanced artificial intelligence algorithms, Add Plate Up In tool is designed to enhance creativity, efficiency, and precision in the culinary world. Whether you are a professional chef, a home cook, or a food blogger, this tool will take your gastronomic creations to a whole new level.One of the standout features of Add Plate Up In is its ability to generate sleek and visually appealing plating designs. With a simple click of a button, users can access a vast library of pre-designed plate setups that cater to a wide range of cuisines and dining styles. From elegant and minimalist dishes to vibrant and eclectic presentations, this tool provides endless options to ensure that every meal is visually stunning.Moreover, Add Plate Up In goes beyond mere aesthetics and offers valuable insights and suggestions for plating. Based on the ingredients and the overall theme of the dish, the tool provides recommendations on complementary colors, textures, and arrangement techniques. This feature is particularly useful for those looking to create harmonious and balanced plates that elevate the dining experience.Another notable aspect of Add Plate Up In is its user-friendly interface. The tool is designed to be intuitive and accessible, allowing both experienced chefs and aspiring cooks to navigate through its features effortlessly. Its drag-and-drop functionality enables users to experiment with different elements of the plate, making it a versatile tool for culinary innovation.In addition to its creative capabilities, Add Plate Up In also offers practical solutions for meal planning and portion control. By inputting the desired number of servings or specific dietary requirements, the tool automatically adjusts the plating suggestions and ingredient quantities accordingly. This feature not only saves time but also reduces food waste, making it an eco-friendly option for both individuals and businesses.Furthermore, Add Plate Up In has a comprehensive database of recipes, ingredients, and nutritional information. Users can easily search for recipes based on criteria such as cuisine, cooking time, or specific dietary needs. The tool also provides detailed nutritional breakdowns for each recipe, allowing individuals to make informed decisions about their meals.The team behind Add Plate Up In has collaborated with renowned chefs and culinary experts to ensure that the tool meets the highest standards of excellence in the industry. They have incorporated years of expertise and feedback into the development of this software, making it a powerful tool for professionals and amateurs alike.With its user-centric approach and commitment to continuous improvement, Add Plate Up In promises to be a game-changer in the culinary world. It empowers individuals to unleash their creativity, streamline their meal preparation process, and enhance the overall dining experience.In conclusion, Add Plate Up In is a revolutionary tool that combines cutting-edge technology with culinary expertise. Its advanced features, user-friendly interface, and practical solutions make it an invaluable asset for chefs, home cooks, and food enthusiasts. Whether you aim to impress guests with visually stunning plates or optimize your meal planning and portion control, Add Plate Up In is the ultimate tool to take your culinary skills to new heights.
Unlock the World of Metal Stamping Die: A Comprehensive Guide
[Assistant]Title: Industry Leader Launches an Innovative Metal Stamping Die, Revolutionizing Manufacturing ProcessesIntroduction: In today's constantly evolving manufacturing industry, technological advancements play a crucial role in improving efficiency and productivity. Addressing this need, a renowned industry leader has unveiled its latest innovation in metal stamping dies, promising to transform manufacturing processes and elevate the quality of end products. With a rich history of expert craftsmanship and a commitment to innovation, this company has consistently raised the bar in the manufacturing sector. This groundbreaking development is set to revolutionize the industry, setting new standards for precision and reliability.[Brand Name], the leading manufacturer of metal stamping solutions, is proud to introduce its newest addition to its lineup of cutting-edge products. Designed with meticulous attention to detail, the company's advanced metal stamping die merges state-of-the-art technology with exceptional craftsmanship. This innovative product eliminates the limitations of conventional manufacturing techniques, effectively optimizing productivity and minimizing downtime.The new metal stamping die is the result of extensive research and development, leveraging [Brand Name]'s years of experience. The company prides itself on its deep understanding of customer needs and its ability to anticipate and adapt to industry trends. As a result, this remarkable metal stamping die has been meticulously engineered to address the challenges faced by manufacturers across various sectors.With its focus on precision, productivity, and durability, this next-generation metal stamping die ensures unparalleled performance, regardless of the complexity of the design or material. The cutting-edge technology incorporated into the die enables enhanced accuracy, making it perfect for producing intricate and high-quality components essential across industries.The new metal stamping die boasts an advanced construction designed to enhance efficiency and long-lasting performance. The die's robust structure minimizes wear and tear and increases tool longevity, significantly reducing downtime due to maintenance or replacement. Furthermore, the die's automated features streamline the production process, effectively increasing output and reducing associated costs.Beyond its inherent technical advancements, this metal stamping die prioritizes the safety of workers operating in manufacturing environments. It incorporates robust safety features that mitigate potential hazards and improve overall operational safety standards. This commitment to creating a secure working environment demonstrates [Brand Name]'s dedication to its customers' welfare and sets it apart from competitors.As with all [Brand Name]'s products, this metal stamping die adheres to strict quality control measures to ensure reliability and consistency. The company's unwavering commitment to delivering excellence is reflected in its rigorous testing procedures, guaranteeing that each die meets the highest industry standards. This commitment to quality assurance has earned the company a renowned reputation for its products' reliability and longevity.In conclusion, the introduction of the new metal stamping die by [Brand Name] marks a significant milestone in the manufacturing industry. By combining cutting-edge technology, uncompromising craftsmanship, and a commitment to customer satisfaction, the company has created a revolutionary product that redefines precision, productivity, and safety. With this innovation, [Brand Name] is set to empower manufacturers worldwide, streamlining their processes, increasing efficiency, and delivering exceptional products that exceed industry expectations.As a frontrunner in the manufacturing sector, [Brand Name] continues to drive innovation and shape the future of the industry. With each groundbreaking development, the company solidifies its position as the go-to provider of cutting-edge metal stamping solutions, consistently surpassing the needs and expectations of its customers.
Essential Guide to CNC Milling Parts: Everything You Need to Know
Title: Revolutionizing Precision Manufacturing: CNC Milling Parts and Innovative SolutionsIntroduction:Precision manufacturing has always been an integral component of various industries, facilitating the production of complex parts and components with utmost accuracy and efficiency. Among the many techniques and technologies involved in this field, CNC milling parts have emerged as a cutting-edge solution that has revolutionized the manufacturing industry. With its ability to meticulously shape materials into intricate designs while minimizing downtime and ensuring consistent quality, CNC milling parts have become a game-changer for numerous businesses worldwide. In this article, we will explore the significant advancements made by CNC milling parts and their impact on the manufacturing landscape.1. Overview of CNC Milling Parts:CNC milling is a computer-controlled process that utilizes rotating cutting tools to remove material from a workpiece and transform it into a desired shape or form. The parts used in this process, commonly known as CNC milling parts, consist of various components such as cutting tools, machine spindles, workholding mechanisms, and computer numerical control systems. These parts work synchronously to optimize precision, speed, and flexibility in the manufacturing process.2. Unparalleled Precision:CNC milling parts have gained a reputation for their unparalleled precision, enabling the production of highly intricate and complex designs with microscopic accuracy. By utilizing advanced software and CAD/CAM integration, manufacturers can achieve precise measurements and intricate tool paths that were once considered unattainable. This precision opens up unprecedented opportunities for industries that require intricate components, such as aerospace, medical, and automotive sectors.3. Enhanced Efficiency:The integration of CNC milling parts into manufacturing processes has significantly enhanced efficiency and productivity. With the ability to perform multiple machining operations without recalibration and operator intervention, CNC milling parts minimize downtime, increase throughput, and reduce human error. Additionally, these parts offer quick setup times, high-speed machining capabilities, and the potential for lights-out operations, ensuring optimal utilization of both time and resources.4. Versatility:CNC milling parts offer remarkable versatility, enabling manufacturers to work with various materials including metals, plastics, composites, and even wood. The ability to customize cutting parameters, tooling, and workholding systems allows for the precise machining of a wide range of materials, expanding the possibilities for different industrial applications. From producing intricate gears for the automotive industry to crafting delicate medical implants, CNC milling parts enable manufacturers to meet diverse market demands.5. Quality Control:Ensuring consistent quality is paramount in the manufacturing sector, and CNC milling parts have played a pivotal role in achieving this goal. By utilizing advanced sensors and monitoring systems, these parts allow for real-time feedback and automatic adjustments during the milling process, ensuring adherence to specified dimensions and quality control standards. Moreover, CNC milling parts reduce manual intervention, minimizing the risk of human errors that may compromise the quality of final products.6. Sustainable Manufacturing:In recent years, sustainability has become a crucial aspect of the manufacturing industry. CNC milling parts have contributed to sustainable manufacturing practices by minimizing material waste, energy consumption, and environmental impact. Computer-controlled operations enable optimal material usage, reducing scrap and conserving resources. Additionally, CNC milling parts facilitate the use of eco-friendly cutting fluids and lubricants, ensuring responsible waste management and efficient coolant recycling.Conclusion:CNC milling parts have revolutionized the precision manufacturing industry, introducing unprecedented levels of accuracy, efficiency, and versatility. From intricate designs to mass production capabilities, these parts have transformed the way industries across the globe approach their manufacturing processes. As technology continues to advance, CNC milling parts are likely to play a pivotal role in shaping the future of precision manufacturing, enabling businesses to achieve new heights in terms of quality, productivity, and sustainability.
Boost Efficiency and Precision with Metal Stamping: A Complete Overview
[Editor's Note: The brand name has been removed from the content below.]Tool Metal Stamping: A Precision Manufacturing Solution to Elevate Efficiency Introduction:In today's competitive business landscape, companies are constantly striving to enhance their production processes and deliver high-quality products. Precision manufacturing techniques play a vital role in achieving these goals, and one such technique is Tool Metal Stamping. This innovative approach revolutionizes manufacturing by enabling companies to create complex parts and components with exceptional accuracy and efficiency. Tool metal stamping is a highly precise method used in various industries, including automotive, aerospace, electronics, and telecommunications, to name a few. This technique involves the creation of intricate metal parts by applying high-pressure force on metal sheets, resulting in a finished product that meets the strictest industry standards. Companies have recognized the immense potential of tool metal stamping and are increasingly adopting this technology to streamline their operations and gain a competitive edge. By leveraging the benefits offered by tool metal stamping, businesses can achieve enhanced productivity, durability, and cost-effectiveness in their manufacturing processes.Enhanced Productivity: Tool metal stamping enables manufacturers to produce complex parts with incredible precision, significantly reducing the need for manual labor and minimizing the risk of human error. Automated systems and advanced software in tool metal stamping processes ensure consistent and accurate component production, which directly translates into increased productivity. Manufacturers can meet stringent production timelines while maintaining high-quality standards, leading to improved overall productivity and customer satisfaction.Durability and Efficiency:Tool metal stamping offers exceptional durability, giving products the ability to withstand harsh environmental conditions and extensive use. The high-pressure applied during the manufacturing process ensures that the finished parts are resilient and less prone to wear and tear. This makes tool metal stamping ideal for applications requiring robust components, such as automotive bodies, consumer appliances, or aerospace structures. Moreover, the efficient use of materials in the stamping process minimizes waste, promoting sustainability and reducing costs.Cost-Effectiveness:By integrating tool metal stamping into their manufacturing processes, companies can significantly reduce costs associated with labor, material waste, and quality control. The automated nature of tool metal stamping eliminates the need for manual labor, reducing labor costs and the risks of human error. Additionally, the efficient use of materials ensures minimal waste and decreases material expenses. The precision achieved through tool metal stamping reduces the need for quality control inspections and rework, resulting in further cost savings.Market Advantages:With the growing demand for intricate parts and components in various industries, companies employing tool metal stamping gain a considerable advantage in today's competitive market. The ability to manufacture intricate designs at high volumes and tight tolerances sets companies apart from competitors who rely on traditional manufacturing methods. The versatility of tool metal stamping enables businesses to cater to the diverse needs of their customers, ensuring customer satisfaction and loyalty. By embracing tool metal stamping, companies position themselves as leaders in innovation and precision manufacturing.Conclusion:The implementation of tool metal stamping in manufacturing processes has revolutionized the industry by offering exceptional precision, increased productivity, durability, cost-effectiveness, and market advantages. This advanced technique enables companies to meet the demands of a fast-paced market while delivering high-quality products consistently. As businesses continue to explore the potential of tool metal stamping, its significance in precision manufacturing is set to grow, contributing to the industry's evolution towards streamlined and efficient production processes.
Discover the Key Benefits of Form Inspection Gage for Streamlined Processes
Form Inspection Gage Enhances Quality Control in Manufacturing ProcessesIn today's rapidly evolving manufacturing industry, ensuring the highest level of quality control has become paramount for companies aiming to thrive in the competitive market. To address this need, technological advancements have led to the development of the Form Inspection Gage, a cutting-edge solution that revolutionizes quality assurance in manufacturing processes. This innovative tool, created by a leading engineering company, has gained widespread recognition for its ability to enhance the accuracy and effectiveness of inspections, empowering manufacturers to deliver superior products to their consumers.With the manufacturing sector experiencing significant advancements, the Form Inspection Gage has emerged as a game-changer for companies striving to uphold their reputation for producing high-quality goods. By utilizing advanced scanning technology, this tool can precisely measure and inspect components, ensuring that they meet the stringent quality standards set by the manufacturer. The gage accurately captures even the most intricate details of a product, providing manufacturers with invaluable data to monitor and improve their production processes.The accumulated data generated by the Form Inspection Gage allows manufacturers to monitor key manufacturing parameters such as product dimensions, geometric features, and surface imperfections. By providing a comprehensive analysis of these parameters in real-time, the gage enables manufacturers to identify any deviations from the desired specifications promptly. This early detection not only helps in reducing scrap, rework, and unnecessary production costs but also ensures that only products meeting the highest quality standards reach the market.One of the notable features of the Form Inspection Gage is its ability to detect minuscule defects that are often invisible to the naked eye. By leveraging advanced algorithms and cutting-edge software, the gage can accurately detect even the tiniest surface imperfections, such as scratches or dents. Additionally, the tool can identify deviations in product dimensions, ensuring that each component aligns perfectly with the desired specifications. By identifying these defects early on, manufacturers can rectify issues promptly, thereby preventing costly recalls or customer dissatisfaction.Furthermore, the Form Inspection Gage streamlines the inspection process, enhancing the overall productivity of manufacturing operations. Traditionally, manual inspections are time-consuming and prone to human error. With this new technological advancement, however, inspections can be carried out swiftly and efficiently, resulting in increased production throughput and reduced labor costs. Moreover, the gage's user-friendly interface allows even non-technical personnel to operate the tool, further optimizing operational efficiency across the manufacturing floor.The Form Inspection Gage also integrates seamlessly into existing manufacturing processes, minimizing disruption and ensuring a seamless transition. The tool is compatible with various production lines, regardless of the industry or product type, making it an ideal solution for manufacturers from diverse sectors. Additionally, the gage can be easily calibrated and configured to adapt to the specific requirements of each manufacturing operation, further enhancing its versatility and usability.In conclusion, the Form Inspection Gage has emerged as a cutting-edge solution that significantly enhances quality control in manufacturing processes. By leveraging advanced scanning technology, this tool enables manufacturers to accurately measure and inspect products, ensuring that they adhere to the highest quality standards. Its ability to detect minuscule defects, streamline the inspection process, and seamlessly integrate into existing manufacturing operations has transformed the way manufacturers approach quality assurance. As industries continue to evolve, the Form Inspection Gage is poised to play a pivotal role in driving excellence and ensuring customer satisfaction in the manufacturing sector.
Why Cowls Are Essential for Your Safety and Comfort
Title: Innovative Vehicle Safety Startup Revolutionizes Automotive Industry Introduction: In today's ever-evolving world, automotive safety has become a top priority for both manufacturers and consumers. One promising company, Cowl Die, is leading the charge in this area, introducing groundbreaking technologies that are reshaping the automotive industry. With their dedication to innovation and commitment to advancing vehicle safety, Cowl Die is poised to revolutionize the way we all travel on the roads.[Paragraph 1: 150 words]Cowl Die, an emerging industry player, has emerged with a mission to redefine the concept of vehicle safety through technological advancements and intelligent design solutions. Founded in collaboration with industry experts and engineers, this company has quickly gained recognition for its groundbreaking innovations and dedication to ensuring passenger safety.[Paragraph 2: 150 words]Cowl Die's groundbreaking approach to vehicle safety centers around the development of cutting-edge technologies that increase occupant protection, enhance vehicle collision avoidance, and advance overall road safety. By integrating state-of-the-art sensors, advanced imaging systems, and artificial intelligence, Cowl Die's products have the potential to drastically reduce the number of accidents and fatalities on the road.[Paragraph 3: 150 words]One of the key products that Cowl Die has developed is an advanced collision detection system capable of accurately assessing potential hazards and warning drivers in real-time. By employing a combination of radar, lidar, and computer vision technologies, this system offers a comprehensive safety solution that mitigates the risk of collisions and empowers drivers to make informed decisions, ultimately saving lives.[Paragraph 4: 150 words]The dedication to safety doesn't stop at the individual vehicle level. Cowl Die is also spearheading projects aimed at improving road infrastructure and implementing vehicle-to-vehicle communication systems. These initiatives showcase the company's commitment to creating a comprehensive safety ecosystem that encompasses all aspects of the automotive industry.[Paragraph 5: 150 words]Moreover, Cowl Die doesn't just focus on personal vehicles; they also aim to redefine commercial transportation safety standards. By working closely with trucking companies and fleet operators, Cowl Die is developing advanced driver assistance systems specifically tailored to commercial vehicles. These systems are designed to reduce the risk of accidents, enhance driver awareness, and minimize damages to both vehicles and cargo.[Paragraph 6: 50 words]In conclusion, Cowl Die is revolutionizing the automotive industry through its unwavering commitment to vehicle safety. By pushing the boundaries of technology and utilizing cutting-edge innovations, this company is driving the industry forward and shaping a future where road accidents are a thing of the past.Note: The content has been adjusted to remove the brand name as requested.
Essential Guide to CNC Machining Parts: Enhance Productivity and Precision
Title: CNC Machining Parts: Precision Engineering for Specialized IndustriesIntroduction:In today's highly specialized industries, CNC machining has emerged as a vital component in the production process. Renowned for its precision and versatility, CNC machining parts have revolutionized manufacturing, creating opportunities for companies to create intricate and complex designs with unparalleled accuracy. In line with this trend, (Company Name), a leading provider of CNC machining parts, continues to innovate and provide cutting-edge solutions to various industries.Company Overview:Founded in (Year), (Company Name) has rapidly established itself as a trusted name in the CNC machining industry. With a focus on precision engineering, the company prides itself on offering a comprehensive range of CNC machining parts that cater to the diverse needs of industries such as automotive, aerospace, electronics, and many others. Backed by a team of highly skilled engineers and state-of-the-art facilities, (Company Name) aims to deliver superior quality products and exceptional customer service.News Content:1. Expansion of CNC Machining Capabilities:(City, Month and Year) - (Company Name) announced the expansion of its CNC machining capabilities to meet the increasing demand for precision-engineered parts. The company has invested in advanced machinery and equipment, expanding its production capacity to offer even more diverse and intricate CNC machining parts. With this expansion, (Company Name) is poised to serve a wider range of industries and cater to their specific requirements.2. Introduction of Advanced Material Processing:(City, Month and Year) - (Company Name) unveiled its latest breakthrough in CNC machining parts by introducing advanced material processing techniques. By leveraging innovative technologies, the company can now offer precision-engineered parts made from materials that were traditionally challenging to machine, including titanium alloys, high-temperature alloys, and composites. This development opens up new possibilities for industries seeking specialized components that can withstand extreme conditions.3. Enhanced Quality Control Measures:(City, Month and Year) - With a strong commitment to delivering unmatched product quality, (Company Name) has implemented enhanced quality control measures. The company has introduced cutting-edge inspection techniques, including non-destructive testing and rigorous dimensional analysis. These measures ensure that each CNC machining part leaving the facility meets the strictest quality standards, positioning (Company Name) as a reliable partner for industries where precision and reliability are paramount.4. Focus on Sustainability:(City, Month and Year) - Acknowledging the importance of sustainability in today's manufacturing landscape, (Company Name) has prioritized eco-friendly practices. By adopting energy-efficient machining processes and reducing waste generation, the company aims to minimize its environmental impact. Furthermore, (Company Name) actively collaborates with its clients to develop innovative solutions that contribute to a greener future while maintaining the highest standards of precision and quality.5. Dedicated Research and Development:(City, Month and Year) - (Company Name) has established a dedicated research and development department, whose primary focus is innovation and continuous improvement. The team is tasked with exploring new technologies, materials, and process optimization techniques, ensuring that (Company Name) remains at the forefront of the industry. By proactively investing in R&D, the company aims to provide its clients with cutting-edge solutions that push the boundaries of CNC machining.Conclusion:As the demand for precision-engineered parts continues to grow, (Company Name) remains committed to its mission of delivering high-quality CNC machining parts to specialized industries. With its expanding capabilities, commitment to sustainability, and a relentless focus on innovation, (Company Name) is poised to meet the evolving needs of its clients while positioning itself as a leader in the CNC machining industry.
Assembly Checking Fixtures: Ensuring Precise Fit and Quality Control
Title: Revolutionary Assembly Checking Fixtures Enhance Manufacturing EfficiencyIntroduction:In today's rapidly evolving manufacturing industry, companies are continuously seeking innovative solutions to enhance production efficiency and quality assurance. Leading the charge is a renowned manufacturer that specializes in Assembly Checking Fixtures, a cutting-edge technology designed to streamline assembly processes and ensure flawless outcomes. With a commitment to revolutionizing the manufacturing landscape, this company has consistently introduced state-of-the-art solutions that guarantee precision, reduce costs, and maximize productivity for businesses across industries. Body:1. Overview of Assembly Checking Fixtures:This article explores the game-changing Assembly Checking Fixtures, a ground-breaking technology that has become a game-changer in the manufacturing sector. These fixtures are specially designed to verify the accuracy and quality of assembled components in various industries such as automotive, aerospace, and consumer electronics. Assembly Checking Fixtures significantly reduce development costs, minimize rework, and eliminate potential errors early in the assembly process.2. Benefits of Assembly Checking Fixtures:By incorporating Assembly Checking Fixtures, companies gain several benefits that contribute to increased efficiency and improved production outcomes. These fixtures offer precise measurements, which allow for rapid identification of any deviation in assembly, ensuring alignment with design specifications. This early detection saves valuable time and resources by minimizing the need for reassembly or correction later in the production cycle.Moreover, Assembly Checking Fixtures not only identify physical defects but also highlight design flaws, resulting in improved product design and reduced future rework. By identifying issues promptly, companies can implement necessary modifications and adjustments, leading to a streamlined and error-free production process.3. Streamlining Manufacturing Processes:Assembly Checking Fixtures revolutionize assembly line operations by reducing manual inspection and speeding up the production process. Instead of relying solely on human operators to identify errors, these fixtures enable the use of automated systems that accurately assess the quality of assembled components. This not only eliminates human error but also reduces the time and cost associated with conducting manual inspections.Furthermore, Assembly Checking Fixtures aid in achieving batch consistency and adherence to quality standards. By guaranteeing uniformity across all products, this technology ensures customer satisfaction and helps maintain a reliable reputation in the market.4. Industry Applications:Assembly Checking Fixtures find applications in diverse industries, including automotive, aerospace, and consumer electronics. In the automotive sector, these fixtures play a pivotal role in ensuring the accuracy of various components, such as body panels, engine parts, and electrical systems. By using Assembly Checking Fixtures, automotive manufacturers can uphold stringent quality standards and enhance product reliability.In the aerospace industry, where precision and accuracy are of utmost importance, Assembly Checking Fixtures contribute to flawless assembly of critical components such as turbine blades, structural frameworks, and electronic systems. Aerospace manufacturers rely on this technology to guarantee airworthiness, safety, and optimal performance of aircraft.Likewise, consumer electronics manufacturers employ Assembly Checking Fixtures to ensure impeccable assembly of intricate and technologically advanced devices such as smartphones, tablets, and laptops. By utilizing these fixtures, companies can enhance product quality, reliability, and customer satisfaction.5. Future Prospects and Innovations:The acquisition of Assembly Checking Fixtures has become a necessity for modern manufacturing facilities aiming to enhance production efficiency and maintain a competitive edge. As technology continues to evolve, this company remains at the forefront, dedicated to continuously improving Assembly Checking Fixtures with innovations such as advanced sensor technologies, integration with artificial intelligence, and enhanced data analytics capabilities. These advancements will enable manufacturers to further optimize their assembly processes, drive automation, and achieve unparalleled efficiency gains.Conclusion:With the ever-increasing demand for quality and efficiency in the manufacturing industry, Assembly Checking Fixtures have emerged as a game-changing technology. By incorporating these fixtures, companies can ensure precise assembly, adherence to design specifications, and consistent quality throughout the production process. With the continuous advancements in Assembly Checking Fixture technology, the future of manufacturing is poised to witness unprecedented efficiency and productivity gains.
Unveiling the Latest Lathe Components - Enhancing Precision Engineering
Title: Manufacturing Company Introduces New Lathe Components to Enhance Precision and EfficiencyIntroduction:In an exciting development for the manufacturing industry, esteemed company {}, a leading figure in the field of precision engineering, has recently unveiled its latest range of high-quality Lathe Components. With a reputation for delivering innovative solutions that enhance precision and efficiency, {}'s technological advancements have caught the attention of manufacturers worldwide. These cutting-edge Lathe Components are poised to revolutionize the industry, enabling businesses to achieve new levels of accuracy and productivity.Paragraph 1:The newly unveiled Lathe Components by {} demonstrate the company's unwavering commitment to pushing the boundaries of precision engineering. Equipped with state-of-the-art technology, these components offer improved precision, delivering consistent, high-quality results. {} has utilized its expertise to develop resilient and durable components that are engineered to withstand rigorous manufacturing processes, ensuring a longer lifespan and reduced maintenance costs. The innovation-driven design of these Lathe Components guarantees optimal performance, contributing to enhanced productivity and profitability for manufacturers.Paragraph 2:With the manufacturing industry evolving at an unprecedented pace, {} understands the importance of staying ahead of the curve. To meet the expanding needs of modern businesses, {} has made significant advancements in design, material selection, and manufacturing processes for its Lathe Components. By incorporating the latest innovations, such as advanced materials and surface finishing techniques, {} has succeeded in creating components that exhibit exceptional wear and corrosion resistance. This ultimately translates into extended service life, reduced downtime, and increased operational efficiency for manufacturers.Paragraph 3:One of the standout features of {}'s new Lathe Components lies in their compatibility with a wide range of lathe machines. Recognizing the diverse needs of the industry, {} has engineered these components to seamlessly integrate into various lathe models, ensuring easy installation and optimal performance. Whether it's a small-scale workshop or a large-scale production facility, manufacturers can now benefit from the outstanding precision and reliability that these components provide.Paragraph 4:In addition to enhancing precision and compatibility, {} has also prioritized the safety aspect of their Lathe Components. The company has incorporated innovative safety features, ensuring that operators can work with confidence and minimize the risk of accidents. This user-centric approach underscores {}'s commitment to fostering a safe working environment, prioritizing the well-being of operators and maintaining the smooth running of daily operations.Paragraph 5:To bring these revolutionary Lathe Components to market, {} has implemented stringent quality control measures throughout the production process. Adhering to stringent international standards, {} leaves no stone unturned in ensuring that each component meets the highest quality benchmarks. By employing a team of experienced engineers and technicians, {} guarantees that their components deliver exceptional performance, reliability, and durability.Conclusion:With the introduction of their new Lathe Components, {} has once again demonstrated their position as an industry leader in precision engineering. These components have been engineered to support manufacturers in achieving higher levels of accuracy, efficiency, and safety in their operations. {}'s relentless pursuit of innovation has resulted in a remarkable range of Lathe Components that are poised to transform the manufacturing landscape. As manufacturers seek to optimize their processes and remain competitive, the enhanced precision and compatibility offered by these components will undoubtedly play a vital role in shaping the future of the industry.
Discover the Innovative and Efficient World of Robotic Welding Fixtures
Title: Cutting-Edge Robotic Welding Fixture Revolutionizes Industrial Manufacturing Introduction:In a significant milestone for industrial manufacturing, a revolutionary robotic welding fixture has been unveiled by a leading company. This cutting-edge technology marks a critical development in the industry, aiming to enhance productivity, quality, and efficiency in the welding process. The state-of-the-art fixture, designed to remove limitations associated with traditional welding methods, is set to revolutionize how welding operations are conducted in various sectors.Leveraging the latest advancements in robotic automation and precision engineering, this innovative fixture - developed by a pioneering company in the field - offers unparalleled versatility, precision, and ease of use. Let us delve into this groundbreaking achievement that showcases the future of welding.1. Enhanced Precision and Efficiency:The advent of robotic welding fixtures has completely transformed the conventional welding processes. By integrating advanced robotics with computer numerical control (CNC) technology, this fixture offers remarkable precision and repeatability, reducing human error and ensuring consistently high-quality welds. This precision and efficiency significantly minimize material waste, remove the need for rework, and optimize the production output, ultimately leading to cost-effectiveness.2. Flexibility and Adaptability:The universal design of this robotic welding fixture allows it to accommodate a wide range of welding applications, regardless of the industry or product specifications. Its adaptability enables it to work seamlessly with different materials, including steel, aluminum, and alloys. Additionally, the fixture can be customized with specific tooling and accessories, further enhancing its versatility and making it suitable for various projects, ranging from small-scale to large-scale operations.3. Streamlined Workflow and Production:With its ability to automate the welding process, the robotic fixture significantly speeds up production while maintaining exceptional consistency and quality. By eliminating slow and cumbersome manual welding methods, manufacturers can witness a drastic reduction in turnaround time for projects, leading to increased productivity and overall efficiency. This fixture also ensures a smooth workflow as it minimizes the need for manual intervention, allowing personnel to focus on more critical tasks.4. Integrated Software and Control System:The state-of-the-art robotic welding fixture incorporates advanced software and a user-friendly control system, making it accessible to operators at all skill levels. The intuitive interface allows for easy programming, setup, and monitoring of welding parameters, ensuring precise control over the welding process. The software also enables seamless integration with existing manufacturing systems, facilitating data exchange and enhancing the overall efficiency of the production line.5. Employee Safety and Ergonomics:By replacing manual welding with robotic automation, this fixture prioritizes employee safety in welding operations. The automated process eliminates the exposure to hazardous fumes, intense heat, and risks associated with prolonged manual welding. This shift towards automation also reduces physical strain on workers, contributing to improved ergonomics and overall well-being in the workplace.Conclusion:The unveiling of this groundbreaking robotic welding fixture represents a giant leap in industrial manufacturing. With its unparalleled precision, adaptability, and streamlined workflow, the fixture is set to redefine the welding process across various sectors. Apart from enhancing productivity and cost-effectiveness, its integrated software and control systems ensure easy operation while prioritizing employee safety. As this technology becomes more prevalent, industries can embrace the future of welding and witness a significant transformation in their manufacturing capabilities.