Understanding the Body In White Automotive: What You Need to Know
By:Admin
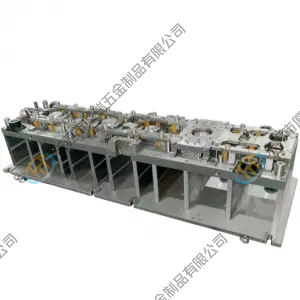
Founded in 1995, Body in White Automotive has continually evolved and expanded its capabilities to meet the ever-changing demands of the automotive market. With a state-of-the-art manufacturing facility and a team of highly skilled engineers and technicians, the company has been able to develop a wide range of advanced automotive components, including body structures, chassis systems, and other key parts.
One of the key factors behind Body in White Automotive's success is their commitment to innovation. The company has invested heavily in research and development, enabling them to stay ahead of the competition and consistently deliver cutting-edge products to their customers. By leveraging the latest technologies and manufacturing processes, Body in White Automotive has been able to produce components that are not only lightweight, but also incredibly strong and durable.
In addition to their focus on innovation, Body in White Automotive is also dedicated to maintaining the highest levels of quality and reliability. The company has implemented strict quality control measures throughout the manufacturing process, ensuring that each component meets the most rigorous industry standards. This commitment to excellence has earned Body in White Automotive a reputation for producing components that are of the highest quality and performance, making them a trusted partner for leading automotive manufacturers around the world.
Furthermore, the company has also placed a strong emphasis on sustainability and environmental responsibility. Body in White Automotive has implemented eco-friendly manufacturing practices and has made significant investments in technologies that minimize their environmental impact. By prioritizing sustainability, the company is not only contributing to a healthier planet, but also meeting the growing demand for greener automotive products.
Body in White Automotive's dedication to excellence and innovation has not gone unnoticed. In recent years, the company has experienced significant growth, expanding its global presence and attracting new customers from diverse segments of the automotive industry. Their commitment to delivering superior products and exceptional service has solidified their position as a trusted partner for automotive manufacturers looking for high-quality components.
Looking ahead, Body in White Automotive is poised to continue its upward trajectory. With a strong focus on research and development, the company is constantly working to develop new technologies and products that will further enhance the performance and efficiency of modern vehicles. By staying at the forefront of the automotive industry, Body in White Automotive is well-positioned to meet the evolving needs of their customers and drive innovation in the market.
In conclusion, Body in White Automotive has established itself as a leading manufacturer of automotive components, with a strong reputation for quality, reliability, and innovation. Through their dedication to excellence and sustainability, the company has experienced significant growth and is well-equipped to continue making a positive impact on the automotive industry. As they move forward, Body in White Automotive is set to remain a driving force in the development of cutting-edge automotive technologies and components.
Company News & Blog
High-Quality 18650 and 26650 Fixtures from China - A Comprehensive Review
Title: Innovative Fixtures for 18650 and 26650 Batteries Set to Revolutionize Manufacturing ProcessesIn today's fast-paced technological world, the demand for efficient and reliable energy storage solutions has never been higher. As the global market for lithium-ion batteries continues to expand, companies are constantly seeking new and innovative ways to streamline their manufacturing processes.In response to these growing demands, the renowned company, [Company Name], has introduced groundbreaking fixtures for 18650 and 26650 batteries. These fixtures are designed to optimize the production processes of lithium-ion batteries, ultimately revolutionizing the way these vital energy storage components are manufactured.The 18650 Fixture and 26650 Fixture are the latest additions to [Company Name]'s impressive lineup of products. These cutting-edge fixtures are engineered to ensure precision and efficiency in the assembly and welding processes of lithium-ion batteries, offering manufacturers a significant competitive advantage in the highly competitive energy storage market.One of the key highlights of the 18650 Fixture and 26650 Fixture is their versatility and adaptability. These fixtures are compatible with a wide range of battery designs and specifications, allowing manufacturers the flexibility to cater to diverse market demands without compromising on quality or efficiency. This adaptability is crucial in the dynamic landscape of lithium-ion battery production, where agility and customization play a pivotal role in meeting the ever-evolving needs of consumers and industries.Moreover, the fixtures' ergonomic and user-friendly design significantly enhances the overall operational efficiency of battery manufacturing processes. By providing easy access to critical assembly and welding points, the fixtures minimize the risk of errors and reduce the time required for each production cycle. This not only boosts productivity but also ensures the consistent quality of the batteries being produced, thereby reinforcing the reputation of manufacturers in the industry.As an industry leader in the development of cutting-edge manufacturing solutions, [Company Name] has established a reputation for delivering high-performance products that redefine industry standards. With the introduction of the 18650 Fixture and 26650 Fixture, the company continues to uphold its commitment to innovation, quality, and customer satisfaction, setting new benchmarks for excellence in lithium-ion battery manufacturing.In addition to their technological prowess, [Company Name] also sets itself apart through its unwavering dedication to customer support and satisfaction. Recognizing that each client has unique needs and challenges, the company offers personalized solutions and comprehensive technical assistance to ensure the seamless integration of its products into diverse manufacturing environments. This customer-centric approach has earned [Company Name] the trust and loyalty of numerous companies worldwide, solidifying its position as a trusted partner in the industry.The impact of the 18650 Fixture and 26650 Fixture extends beyond the realms of manufacturing efficiency and product quality. These fixtures also represent a significant step towards promoting sustainability and environmental responsibility in the energy storage sector. By optimizing the production processes of lithium-ion batteries, the fixtures contribute to the reduction of waste and energy consumption, aligning with global efforts to minimize the ecological footprint of industrial operations.Looking ahead, the introduction of the 18650 Fixture and 26650 Fixture is poised to catalyze a paradigm shift in the way lithium-ion batteries are manufactured. With their unparalleled precision, adaptability, and efficiency, these fixtures are destined to empower manufacturers with the means to meet the escalating demands of the energy storage market while spearheading a new era of innovation and sustainability.In conclusion, the unveiling of the 18650 Fixture and 26650 Fixture by [Company Name] represents a significant milestone in the evolution of lithium-ion battery manufacturing. As the global demand for reliable energy storage solutions continues to soar, these groundbreaking fixtures are poised to redefine industry standards, revolutionize production processes, and uphold the highest levels of quality and efficiency in the production of lithium-ion batteries. With its unwavering commitment to innovation and customer satisfaction, [Company Name] is set to lead the charge in shaping the future of energy storage technology.
Effective CMM Inspection Fixtures for Precise Measurement and Quality Assurance
CMM Inspection Fixtures, also known as Coordinate Measuring Machine Inspection Fixtures, are an essential tool in the manufacturing industry. They are used to ensure the accuracy and precision of the parts being produced, and they play a crucial role in quality control. These fixtures are designed to hold the workpiece in place during the inspection process, allowing for precise and consistent measurements.One company that specializes in the design and manufacture of CMM inspection fixtures is {Company Name}. With over 20 years of experience in the industry, {Company Name} has built a reputation for delivering high-quality, reliable, and innovative solutions to its customers. The company's expertise in fixture design and manufacturing has made it a trusted partner for many leading manufacturers across various industries.{Company Name} takes a comprehensive approach to fixture design, considering factors such as part geometry, material, and inspection requirements. Their team of skilled engineers and designers use the latest CAD/CAM software and advanced machining technologies to create fixtures that meet the highest standards. Additionally, the company offers customization services, ensuring that each fixture is tailored to the specific needs of the customer.In addition to their expertise in fixture design, {Company Name} also provides comprehensive support and training services to their customers. They understand the importance of ensuring that their fixtures are used effectively and efficiently, and they are committed to assisting their customers in achieving the best results.The quality of {Company Name}'s products and services has not gone unnoticed. They have received numerous accolades and certifications, demonstrating their commitment to excellence and customer satisfaction. Their dedication to continuous improvement and innovation has allowed them to stay at the forefront of the industry.With their strong track record and expertise, {Company Name} has become a preferred supplier for many manufacturers seeking high-quality CMM inspection fixtures. Their ability to deliver custom solutions and their commitment to customer support set them apart from their competitors.As the manufacturing industry continues to evolve and demand for precision and quality increases, the need for reliable CMM inspection fixtures will only grow. {Company Name} is well-positioned to meet this demand, thanks to their dedication to excellence, innovation, and customer satisfaction.In conclusion, CMM inspection fixtures are a critical tool in the manufacturing industry, and {Company Name} has established itself as a leader in the design and manufacture of these fixtures. With their expertise, commitment to quality, and dedication to customer support, {Company Name} has become a trusted partner for manufacturers seeking precision and reliability in their inspection processes. As the industry continues to evolve, {Company Name} is poised to continue its success and uphold its reputation as a top supplier of CMM inspection fixtures.
Essential Guide to Effective Welding Fixtures for Superior Results
Title: Revolutionizing Welding Solutions: The Future of Welding FixturesIntroduction:In today's rapidly evolving industrial landscape, innovative solutions in manufacturing processes have become indispensable. One such vital component to streamline manufacturing operations is the welding fixture. A welding fixture greatly enhances precision, productivity, and cost efficiency in welding processes. Recognizing this need, {Company Name}, a leading industrial engineering firm, has recently unveiled their cutting-edge welding fixture technology, poised to revolutionize the welding industry.A Welding Fixture at the Forefront of Technological Advancements:{Company Name}'s new welding fixture represents a remarkable step forward in the field of welding technology. Designed by their team of engineers and welders, this state-of-the-art fixture incorporates advanced features that guarantee unparalleled precision and efficiency.Precision Engineering: The intricate design of the firm's welding fixture ensures precise alignment and tight tolerances during the welding process. This eliminates inconsistencies and irregularities, resulting in uniformly high-quality welds. With this revolutionary fixture, manufacturers will experience increased productivity and reduced material waste caused by rework.Dynamic Functionality: The new welding fixture allows for multi-axis adjustments, enabling welders to work on complex geometries and unconventional joint configurations. This versatility is particularly valuable in various industries, including automotive, aerospace, and construction, where intricate welding operations are common. The fixture's adaptability simplifies the welding process, reduces setup time, and minimizes the risk of errors.Integrated Sensing Technology: Equipped with cutting-edge sensors, the welding fixture actively monitors and controls vital parameters during the welding process. Real-time data on temperature, voltage, and current can be collected, allowing welders to make necessary adjustments instantaneously. With this dynamic feedback loop, manufacturers can optimize the welding conditions, enhance quality control, and ensure consistent results.Streamlined Automation: {Company Name}'s welding fixture seamlessly integrates with robotic welding systems, greatly enhancing automation capabilities. By integrating the fixture into industrial robots, manufacturers can achieve higher precision and efficiency while reducing labor costs. The automated welding solution, combined with the fixture's dynamic functionality, accelerates production rates and reduces cycle times, significantly impacting the bottom line.Customer-centric Approach:{Company Name} has always been committed to offering comprehensive solutions tailored to their clients' specific needs. Demonstrating this commitment, their welding fixture is customizable to suit various welding applications. Whether it is thin sheet welding, pipe welding, or heavy-duty fabrication, their fixture can accommodate a wide range of welding requirements. Additionally, the fixture is compatible with a variety of welding processes, including MIG, TIG, and spot welding.Environmental Considerations:Environmental sustainability is a pressing concern for the manufacturing industry. In line with this issue, {Company Name}'s welding fixture is designed with eco-friendly considerations. The fixture incorporates energy-efficient components and ensures minimal material waste. By optimizing the welding process, the fixture helps reduce harmful emissions and contributes to sustainable manufacturing practices.Conclusion:With their technologically advanced welding fixture, {Company Name} has taken a significant step toward revolutionizing the welding industry. By combining precision engineering, dynamic functionality, integrated sensing technology, and streamlined automation, the firm's fixture sets new benchmarks in the field. With an unwavering commitment to customer satisfaction and a focus on sustainability, {Company Name} continues to pave the way for efficient and environmentally conscious manufacturing processes. As manufacturers increasingly seek optimized welding solutions, {Company Name}'s welding fixture offers an unrivaled opportunity to elevate productivity, increase quality, and embrace the future of welding.
How to Implement Electrical and Pneumatic Design for Your Project
Electrical & Pneumatic Design, in collaboration with a leading engineering company, has recently introduced a groundbreaking new technology that is set to revolutionize the industry. This innovative system, developed by the team at Electrical & Pneumatic Design, promises to enhance efficiency and productivity for businesses across various sectors.With a focus on customized solutions and cutting-edge technology, Electrical & Pneumatic Design has established itself as a leader in the field of engineering and design. The company's strong commitment to innovation and quality has earned it a reputation for delivering top-notch solutions to its clients.The new technology, which has been designed in partnership with a prominent engineering company, represents a major breakthrough in the industry. It combines advanced electrical and pneumatic design elements to create a system that is more efficient, reliable, and cost-effective than any other currently available on the market.By leveraging the latest in engineering and design, this innovative system is able to optimize the performance of electrical and pneumatic systems in a wide range of applications. This includes manufacturing, industrial automation, and process control, among others. The technology's advanced features allow for greater precision, control, and flexibility, ultimately resulting in improved productivity and reduced downtime for businesses that adopt it.The team at Electrical & Pneumatic Design is thrilled to be at the forefront of this exciting development. With years of experience and expertise in the field, the company is well-equipped to bring this cutting-edge technology to market and help businesses unleash their full potential."We are extremely proud to introduce this game-changing technology to the industry," said a spokesperson for Electrical & Pneumatic Design. "Our team has worked tirelessly to develop a system that meets the evolving needs of our clients and delivers unparalleled performance. We are confident that this innovation will have a transformative impact on businesses across various sectors."In addition to its impressive technical capabilities, the new system also offers a user-friendly interface and seamless integration with existing equipment. This makes it easy for businesses to adopt the technology without disrupting their current operations, further enhancing its appeal.Furthermore, Electrical & Pneumatic Design's commitment to customer satisfaction means that the company provides comprehensive support and maintenance services for its new technology. This ensures that clients can continue to experience the full benefits of the system long after its initial implementation.As the industry continues to evolve, Electrical & Pneumatic Design remains dedicated to pushing the boundaries of what is possible in electrical and pneumatic design. The company's forward-thinking approach and dedication to providing innovative solutions set it apart as a trusted partner for businesses seeking to stay ahead of the curve.With the introduction of this groundbreaking new technology, Electrical & Pneumatic Design is poised to further solidify its reputation as a leading provider of cutting-edge engineering solutions. As businesses increasingly recognize the need for advanced, reliable systems, the company is well-positioned to meet this demand and continue driving innovation in the industry.In conclusion, the team at Electrical & Pneumatic Design, in collaboration with a renowned engineering company, has unveiled a revolutionary new technology that is poised to transform the industry. By harnessing the power of advanced electrical and pneumatic design, this innovative system promises to deliver unparalleled performance, efficiency, and reliability for businesses across various sectors. With its user-friendly interface, seamless integration, and comprehensive support services, the technology is set to become a game-changer for businesses seeking to stay ahead of the curve in a rapidly evolving landscape. So businesses are encouraged to explore the possibilities of this cutting-edge technology to unlock new levels of productivity and success.
Advanced Robotic Machining Techniques for Precision Manufacturing
Robotic Machining Offers Cutting-Edge Manufacturing SolutionsIn the ever-evolving landscape of manufacturing, companies are constantly searching for innovative and efficient solutions to meet the increasing demands of their customers. One such solution that has been gaining traction in the industry is robotic machining, a cutting-edge technology that is revolutionizing the way products are manufactured.Robotic machining, also known as automated machining, is the process of using robots to perform various machining operations such as milling, drilling, grinding, and cutting. These robots are equipped with sophisticated tools and programming that allow them to perform tasks with a level of precision and speed that is unmatched by traditional machining methods.One company at the forefront of this technology is {Company Name}, a leading provider of advanced manufacturing solutions. With a proven track record of delivering high-quality products and exceptional customer service, {Company Name} has established itself as a trusted partner for companies looking to elevate their manufacturing capabilities.{Company Name} offers a wide range of robotic machining solutions that are tailored to meet the specific needs of their customers. Whether it's a small batch of custom parts or a large-scale production run, their team of experts can design and implement a robotic machining system that will deliver exceptional results.The benefits of robotic machining are numerous. By automating the machining process, companies can significantly reduce their production times, improve product consistency, and minimize the risk of human error. This not only leads to higher productivity and cost savings, but also allows companies to take on more complex and challenging projects that may have been previously unfeasible.In addition to these tangible benefits, robotic machining also offers a safer working environment for employees. By removing workers from potentially hazardous machining operations, companies can reduce the risk of workplace accidents and improve overall employee morale and satisfaction.Moreover, robotic machining can also help to address some of the common challenges that the manufacturing industry faces, such as skilled labor shortages and rising labor costs. By relying on automation, companies can reduce their dependence on skilled machinists and allocate their workforce to other areas of their operations where they are needed most.{Company Name}'s commitment to innovation and excellence is reflected in their investment in state-of-the-art robotic machining technology. They continuously strive to stay ahead of the curve by incorporating the latest advancements in robotics and automation into their manufacturing processes, ensuring that their customers always have access to the best solutions available.Furthermore, their dedication to quality is evident in their rigorous quality control measures, which guarantee that every product that leaves their facility meets the highest standards of precision and reliability. This attention to detail has earned them a reputation as a trusted partner for companies in a wide range of industries, including aerospace, automotive, medical, and consumer goods.As the manufacturing industry continues to evolve, the importance of embracing new technologies such as robotic machining cannot be overstated. Companies that are able to adapt and leverage these advancements will be well-positioned to thrive in an increasingly competitive marketplace.With its proven track record, commitment to excellence, and dedication to innovation, {Company Name} is well-equipped to lead the charge in the adoption of robotic machining solutions. By partnering with them, companies can gain a competitive edge and stay ahead of the curve in a rapidly changing industry.In conclusion, robotic machining is a game-changing technology that is reshaping the manufacturing landscape. Companies that understand the value of automation and innovation, and are willing to embrace these advancements, will be best positioned to succeed in the future. And with the expertise and resources of a trusted partner like {Company Name}, the possibilities are endless.
How to Use the Front Floor Panel Tool for Efficient Home Repairs
Front Floor Panel Tool Revolutionizes Automotive Manufacturing ProcessThe automotive industry is constantly evolving, with manufacturers always on the lookout for innovative tools and technologies that can streamline their production processes and improve the quality of their vehicles. One such innovative tool making waves in the industry is the Front Floor Panel Tool, which is revolutionizing the way automotive companies produce their vehicles. This groundbreaking tool, developed by a leading automotive manufacturing company, is set to change the game for the entire industry.The Front Floor Panel Tool, created by a team of expert engineers and designers, is specifically designed to improve the manufacturing process of front floor panels for vehicles. This tool is capable of shaping, cutting, and molding front floor panels with unparalleled precision and efficiency. Its state-of-the-art technology allows for the production of front floor panels that are not only visually appealing but also durable and long-lasting.One of the key features of the Front Floor Panel Tool is its ability to work with a wide range of materials, including steel, aluminum, and composite materials. This flexibility makes it suitable for use in the production of various types of vehicles, from compact cars to heavy-duty trucks. Additionally, the tool is equipped with advanced automation and robotics systems, which further enhance its efficiency and accuracy.The implementation of the Front Floor Panel Tool has already had a significant impact on the manufacturing process at the company's facilities. By streamlining and optimizing the production of front floor panels, the tool has significantly reduced production times and increased overall productivity. This has not only allowed the company to meet the growing demand for their vehicles but has also improved the quality and consistency of their products.Furthermore, the Front Floor Panel Tool has also had a positive impact on the company's bottom line. The reduction in production times and the increased efficiency has translated to lower manufacturing costs and improved profit margins. This, in turn, has allowed the company to invest in further research and development, as well as in the expansion of their production capacity.In addition to its impact on the company's operations, the Front Floor Panel Tool has also garnered attention from other players in the automotive industry. Several leading automotive manufacturers have expressed interest in incorporating this innovative tool into their own production processes. This further solidifies the tool's status as a game-changer in the industry.The success of the Front Floor Panel Tool is a testament to the company's commitment to innovation and excellence in automotive manufacturing. With a strong focus on research and development, as well as a dedication to staying ahead of the curve, the company has established itself as a leader in the industry. The creation of the Front Floor Panel Tool is just one example of the company's ongoing efforts to push the boundaries of automotive manufacturing.Looking ahead, the company plans to continue refining and improving the Front Floor Panel Tool, as well as developing other innovative technologies to further enhance their production processes. With a strong track record of success and a forward-thinking approach, the company is well-positioned to make a lasting impact on the automotive industry for years to come.In conclusion, the Front Floor Panel Tool is a game-changer in the automotive industry, revolutionizing the way front floor panels are manufactured. Its advanced technology, unmatched precision, and efficiency have already made a significant impact on the company's operations, as well as garnered interest from other players in the industry. With a strong focus on innovation and a dedication to excellence, the company behind the Front Floor Panel Tool is set to continue leading the way in automotive manufacturing.
Increase Efficiency with a Welding Cell: A Complete Guide
Welding Cell Revolutionizes Manufacturing Process(Welding, a common process in the manufacturing industry, has always been a crucial step in the production of various products. With the advancement of technology, welding has also evolved, giving birth to more efficient and productive methods. One of the recent innovations in welding technology is the introduction of the Welding Cell, a cutting-edge system that has revolutionized the manufacturing process.)The Welding Cell, developed by a leading manufacturing solutions provider, {company name}, is a state-of-the-art system that combines robotics, advanced welding technology, and intelligent software to streamline the welding process. This innovative system is designed to improve the overall efficiency, productivity, and quality of welding operations in various manufacturing industries.The Welding Cell is equipped with a high-precision robotic arm that is capable of performing complex welding tasks with unparalleled accuracy and consistency. The robotic arm is programmed to execute the welding process with precision, speed, and repeatability, ensuring that each weld is of the highest quality. This level of precision and consistency is difficult to achieve with traditional manual welding methods, making the Welding Cell a game-changer in the manufacturing industry.In addition to the robotic arm, the Welding Cell is also equipped with advanced welding technology that enables it to weld a wide range of materials, including steel, aluminum, and other alloys. The system is capable of performing various welding techniques, such as MIG (Metal Inert Gas) welding, TIG (Tungsten Inert Gas) welding, and resistance spot welding, making it a versatile solution for manufacturers with diverse welding needs.Furthermore, the Welding Cell is integrated with intelligent software that enhances its capabilities and performance. The software allows operators to easily program and control the welding process, monitor the system's performance in real-time, and optimize welding parameters for different applications. This level of automation and control not only simplifies the welding process but also reduces the risk of human error, resulting in higher quality welds and increased productivity.The introduction of the Welding Cell has had a significant impact on the manufacturing industry. Manufacturers who have adopted this innovative system have reported notable improvements in their welding operations, including increased productivity, reduced rework, and improved overall product quality. The Welding Cell has allowed manufacturers to streamline their production processes, minimize downtime, and meet the growing demand for high-quality welded components.One of the key benefits of the Welding Cell is its ability to improve workplace safety. By automating the welding process, the system reduces the need for manual labor in hazardous welding environments, minimizing the risk of workplace accidents and injuries. This is especially important in industries where welding is a critical part of the production process, such as automotive, aerospace, and construction.Furthermore, the Welding Cell has also proven to be a cost-effective solution for manufacturers. By increasing productivity and reducing rework, the system helps manufacturers save time and money in their welding operations. Additionally, the high-quality welds produced by the Welding Cell result in fewer defects and scrap, further contributing to cost savings for manufacturers.Overall, the introduction of the Welding Cell has had a significant impact on the manufacturing industry, revolutionizing the welding process and setting new standards for efficiency, productivity, and quality. With its advanced robotics, state-of-the-art welding technology, and intelligent software, the Welding Cell has become an indispensable tool for manufacturers looking to enhance their welding operations and stay ahead in a competitive market.As manufacturing technology continues to evolve, the Welding Cell stands as a testament to the power of innovation and the positive impact it can have on the industry. By embracing cutting-edge solutions like the Welding Cell, manufacturers can position themselves for success and continue to drive progress in the ever-changing landscape of modern manufacturing.
New Fixture Revolutionizes Industry with Innovative Design and Functionality
Gom Fixture, a leading provider of innovative, high-quality fixtures for a variety of industries, has announced the release of a new product line aimed at revolutionizing the way companies approach their manufacturing processes. With a focus on enhancing efficiency, accuracy, and flexibility, these fixtures are designed to meet the ever-changing demands of modern manufacturing.The company, founded in 2007, has a long-standing reputation for delivering cutting-edge solutions that optimize production workflows and improve overall productivity. With a team of experienced engineers and designers, Gom Fixture has consistently pushed the boundaries of fixture technology to provide its customers with top-of-the-line solutions that address the most complex manufacturing challenges.The new product line, which includes a range of modular fixtures, dedicated to increasing efficiency and reducing lead times in the production process. These fixtures are designed to be highly adaptable, allowing for quick and easy reconfiguration to accommodate changes in production requirements. This versatility ensures that manufacturers can maximize their output while minimizing downtime and production disruptions.In addition to their flexibility, the fixtures are also engineered to deliver exceptional accuracy, ensuring that components are consistently held in the correct position during manufacturing. By maintaining tight tolerances, these fixtures help companies achieve higher levels of precision and quality in their products, ultimately improving customer satisfaction and reducing rework and scrap.Furthermore, the fixtures are designed to be user-friendly, with intuitive interfaces that simplify setup and operation. This ease of use reduces training time and allows operators to quickly familiarize themselves with the fixtures, further contributing to improved efficiency and productivity on the production floor."We are proud to introduce our new line of fixtures, which represents a significant leap forward in manufacturing technology," said a spokesperson for Gom Fixture. "Our team has worked tirelessly to develop these solutions, ensuring that they meet the ever-evolving needs of modern manufacturing operations. We believe that these fixtures will empower companies to achieve new levels of efficiency, accuracy, and flexibility in their production processes."Gom Fixture is committed not only to delivering best-in-class solutions but also to providing exceptional customer support. With a team of dedicated professionals, the company offers comprehensive assistance to help its customers implement and maximize the potential of its fixtures. This level of support ensures that manufacturers can quickly integrate these solutions into their operations and begin reaping the benefits of enhanced efficiency and productivity.The release of these new fixtures reaffirms Gom Fixture's position as a driving force in the manufacturing industry, consistently striving to push the boundaries of what is possible with fixture technology. By leveraging innovative design and engineering, the company continues to set the standard for quality, performance, and reliability in the manufacturing sector.As manufacturers seek to stay competitive in an increasingly demanding market, the need for advanced solutions that can streamline processes and improve performance has never been greater. With the introduction of its new product line, Gom Fixture is poised to empower companies with the tools they need to thrive in this challenging environment. These fixtures represent a significant milestone in the company's ongoing commitment to driving the future of manufacturing, and are set to make a lasting impact on the industry as a whole.
Efficient Rear End Plate Tool for Your Automotive Needs
Innovative Rear End Plate Tool Optimizes Performance and Efficiency for Automotive IndustryIn the fast-paced world of automotive manufacturing, precision and efficiency are imperative for success. A reliable and accurate tool can make a significant difference in the quality of the end product. That's where the innovative Rear End Plate Tool, developed by {}, comes into play. The company, known for its cutting-edge solutions for the automotive industry, has once again proven its dedication to excellence with the creation of this groundbreaking tool.The Rear End Plate Tool is a game changer in automotive manufacturing, providing a seamless and efficient solution for rear end plate assembly. With its advanced technology and precision engineering, this tool is designed to optimize performance and simplify the manufacturing process. Its user-friendly interface and intuitive controls make it easy to operate, while its high-speed functionality ensures rapid and reliable results.One of the key features of the Rear End Plate Tool is its ability to streamline the assembly process. By automating the crucial task of rear end plate installation, this tool eliminates the need for manual labor and minimizes the risk of errors. This not only improves efficiency, but also enhances the overall quality of the assembly, resulting in a superior end product.Another standout feature of the Rear End Plate Tool is its versatility. It is compatible with a wide range of rear end plate designs, making it adaptable to various manufacturing requirements. This flexibility allows automotive manufacturers to utilize the tool across different product lines, maximizing its value and utility.In addition to its technical prowess, the Rear End Plate Tool is also built with durability and reliability in mind. Constructed with high-quality materials and components, it is designed to withstand the demands of heavy-duty industrial use. Its robust design and sturdy construction ensure long-term performance and minimal maintenance, making it a cost-effective investment for automotive manufacturers.The introduction of the Rear End Plate Tool by {} reflects the company's commitment to innovation and customer satisfaction. With its cutting-edge technology and focus on enhancing manufacturing processes, this tool is poised to revolutionize the automotive industry."Here at {}, we are dedicated to pushing the boundaries of what is possible in automotive manufacturing," said [Spokesperson], [Title] of {}. "The development of the Rear End Plate Tool is a testament to our relentless pursuit of excellence and our unwavering commitment to providing our customers with the best solutions available."The Rear End Plate Tool is just one example of the forward-thinking approach that {} brings to the automotive industry. With a track record of delivering innovative and effective solutions, the company continues to set new standards for quality and performance in manufacturing technology.As automotive manufacturers strive for greater efficiency and productivity, the Rear End Plate Tool stands out as a valuable asset. Its unrivaled precision, versatility, and reliability make it an indispensable tool for streamlining the rear end plate assembly process, ultimately contributing to higher productivity and improved product quality.With its successful introduction of the Rear End Plate Tool, {} has once again proven its leadership in the automotive manufacturing sector. As the industry continues to evolve, the company remains at the forefront, driving progress and providing advanced solutions that meet the ever-changing needs of automotive manufacturers worldwide.
Diverse Range of Steel Parts Available for CNC Machining
CNC Steel Parts is a leading manufacturer of precision steel components for various industries around the world. The company, with its state-of-the-art facilities and cutting-edge technology, is known for delivering high-quality products and exceptional customer service.Established in [year], CNC Steel Parts has been a prominent player in the steel manufacturing industry for over two decades. The company's commitment to innovation, quality, and continuous improvement has made it a trusted partner for many businesses in need of precision steel components.With a comprehensive range of CNC machining capabilities, CNC Steel Parts can produce a wide variety of steel parts with intricate designs and tight tolerances. From simple shafts and fasteners to complex aerospace components, the company has the expertise and resources to fulfill any customer's requirements.Furthermore, CNC Steel Parts has a dedicated team of engineers and machinists who are highly skilled and experienced in working with various types of steel, including carbon steel, stainless steel, and alloy steel. This allows the company to meet the diverse needs of its customers across different industries, such as automotive, aerospace, marine, and defense.In addition to its manufacturing capabilities, CNC Steel Parts also offers value-added services, such as CNC turning, milling, grinding, and heat treatment. This comprehensive approach enables the company to provide a one-stop solution for its customers' steel component needs, from design and prototyping to production and finishing.Moreover, CNC Steel Parts is committed to quality and precision in every aspect of its operations. The company adheres to strict quality control measures and rigorous inspection processes to ensure that every part meets the highest standards of accuracy and reliability. This dedication to excellence has earned CNC Steel Parts a reputation for delivering superior products that consistently exceed customer expectations.As a global player in the steel manufacturing industry, CNC Steel Parts has established a strong presence in international markets, serving customers in North America, Europe, Asia, and beyond. The company's extensive network of distribution partners and strategic alliances enables it to reach customers worldwide and provide them with timely and efficient support.Looking ahead, CNC Steel Parts is poised for continued growth and success in the industry. The company remains committed to investing in the latest technology and expanding its manufacturing capabilities to stay at the forefront of innovation. Furthermore, CNC Steel Parts is dedicated to building enduring partnerships with its customers and delivering value-driven solutions that help them achieve their business objectives.In conclusion, CNC Steel Parts is a reputable and reliable manufacturer of precision steel components, known for its cutting-edge technology, exceptional quality, and unwavering commitment to customer satisfaction. With its extensive capabilities and global reach, the company is well-positioned to meet the evolving needs of the steel industry and serve as a trusted partner for businesses seeking high-quality steel parts.